EDM Services – Electric Discharge Machining
At Hacheng Mould Co., Ltd. we excel in providing state-of-the-art Electrical Discharge Machining (EDM) services. Our offerings encompass advanced CNC wire cutting, precise EDM drilling, and specialized EDM drilling processing. We take pride in delivering top-notch micro EDM services, tailored to meet the intricate demands of our diverse clientele. Our commitment to precision and excellence in EDM ensures unparalleled results for every project we undertake.
EDM Services At Hacheng Mould Co., Ltd.
Hacheng Mould Co., Ltd., an AS9100 certified leader in electrical discharge machining (EDM) since 2014, specializes in premium-quality EDM services. Our expertise spans Wire EDM, Small Hole EDM Drilling, Sinker EDM, and Water-jet services. We cater to diverse manufacturing sectors including medical, aerospace, defense, and commercial industries. Renowned for our rapid turnaround and competitive pricing, Hacheng is committed to exceeding client expectations with our skilled team. Contact us for a complimentary estimate and quote on our exceptional EDM solutions.
What is EDM?
Electrical Discharge Machining (EDM) is a manufacturing process where a desired shape is obtained using electrical discharges (sparks). Material is removed from the workpiece by a series of rapidly recurring current discharges between two electrodes, separated by a dielectric liquid and subject to an electric voltage. This process allows for the creation of intricate shapes and fine details in materials that are electrically conductive, and is commonly used in complex or hard-to-machine components. EDM is particularly useful in the production of molds, dies, and precision parts in various industries.
Applications requiring fine precision or complicated geometries, such those in the aerospace, automotive, defense, extrusion, electronics, food and beverage, medical, and stamping industries, are a perfect fit for Electrical Discharge Machining (EDM). Metal disintegration machining is an additional facet of EDM. Manufacturers employ discharge machines in this procedure to get rid of broken tool pieces that are stuck inside a workpiece. Bolts, drill bits, taps, and studs are some of these tool pieces. Manufacturers are able to recover or recycle the workpiece’s material by removing them from its core.
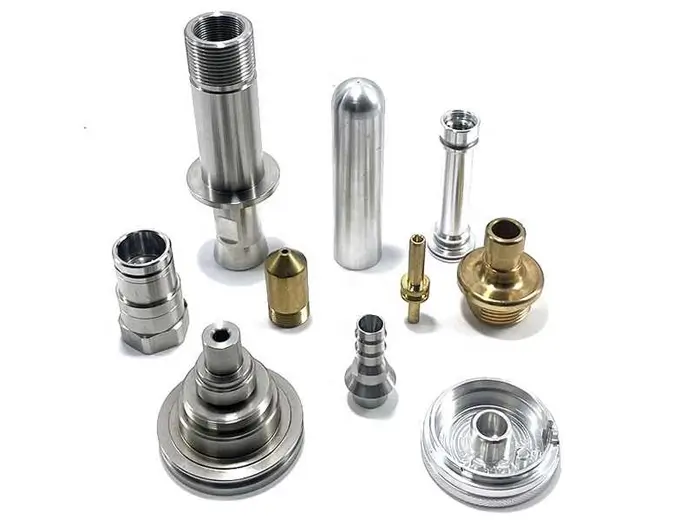
Benefits of the EDM Machining Process
Benefits of the EDM Machining Process include:
- Ability to Machine Complex Shapes: EDM can create intricate and detailed components that are challenging to achieve with conventional machining.
- No Direct Contact: The tool does not make physical contact with the workpiece, reducing mechanical stress.
- High Precision: EDM offers very high accuracy and precision.
- Versatility in Materials: It can machine hard, brittle, or fragile materials without distortion.
- Fine Surface Finish: EDM provides a high-quality surface finish, reducing the need for additional processing.
Versatile Applications of EDM in Manufacturing
EDM is employed by manufacturers for producing molds, tools, and dies essential for molding and casting processes, particularly in plastic mold manufacturing. It’s also instrumental in fabricating compressor blades and various engine components. This technology extends to the creation of delicate items like jewelry, badges, and coins. Additionally, EDM is pivotal in developing prototypes for clients across automotive, aerospace, and electronics sectors, showcasing its versatility and precision in crafting complex and detailed components.
Design Considerations
When designing for EDM (Electrical Discharge Machining), consider the following:
- Material Conductivity: Ensure materials are electrically conductive.
- Tolerance Levels: Design for high precision, as EDM can achieve very fine tolerances.
- Complexity and Detail: Utilize EDM’s capability to create intricate and complex shapes.
- Surface Finish: Plan for the surface finish EDM can achieve, which may reduce the need for post-processing.
- Thermal Stress: Account for minimal thermal stress, as EDM does not generate significant heat in the workpiece.
- Tool and Electrode Design: Design electrodes for the EDM process, considering factors like wear and shape reproduction.
Materials and Types of EDM:
Materials suitable for EDM include any electrically conductive materials such as metals, alloys, and some graphite composites. The types of EDM processes include Wire EDM, where a thin wire is used as an electrode to cut through material; Sinker EDM, where a pre-shaped electrode is used to create complex geometries; and Hole Drilling EDM, specialized for creating small, deep holes with precision. Each type caters to different manufacturing needs, from intricate designs to precision drilling.
Wire EDM:
Maximum dimensions and weight of the work piece: 735 x 530 x 400 mm, 1000 kg
Axis movements: 400 mm X, 300 mm Y, 400 mm Z
30 degrees is the maximum taper.
Hole Popping EDM:
Hole diameters: 0.30-4.0mm
Maximum work piece height: 260mm
Maximum work piece weight: 310kg
Micro EDM:
- CNC micro EDM hole drilling as small as 10 micron (0.0004in) dia.
- Precision small hole drilling services up to 5mm dia.
- Micro EDM sinking operations.
- Micro EDM milling.