S
E
R
V
I
C
E
O
V
E
R
V
I
E
W
Wire EDM Services
Electrical discharge machining, also known as EDM, is a process that uses sparks to cut shapes out of a workpiece.
Hacheng Mould offers sinker and wire EDM machining services whether you need a single part, batch of prototypes, or a production order.
- Various materials.
- Fast delivery.
- 100% quality guaranteed.
Cooperation Brand
Advantages of Wire EDM
- Capable of creating precise, sharp interior angles.
- Perfectly suited for components with slender walls.
- Optimal for metals that are traditionally hard to machine.
- Ensures a smooth finish with no burrs.
Wire EDM Design Considerations
- The material needs to be capable of conducting electricity.
- Surface finishes typically range from 16 to 64 microinches.
- The kerf width generally varies from 0.001 inches to 0.012 inches.
- Edges will have a smooth yet matte finish.
Swift Precision: Surprisingly Quick Custom Wire EDM Deliveries
For your wire EDM parts, Hacheng Mould Co. Ltd., provides immediate quotations in addition to wire EDM service. Together, you and our customer support team will make sure your design requirements are fulfilled.To easily order your part, simply follow these steps:
Construct or upload a CAD file.Create your parts using our free CAD software or by uploading your own CAD, PDF, or picture files.
Set up your component. Choose from more than 20 different surface treatments and materials. Provide the machinist with the quantity, address, and any additional remarks.
Obtain a quotation.Request a price for your design using our CAD system right away.
Place your components order.Order now to get your high-quality CNC components!
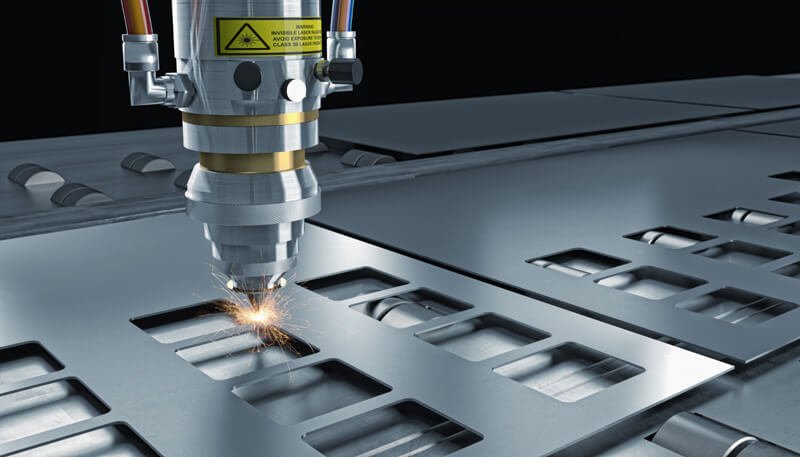
In machining, what does EDM stand for?
Electrical discharge machining, or wire electrical discharge, is referred to as EDM. It is an extremely precise method of fabricating metal that uses a tiny wire and a voltage between 50 and 300 volts to cut through metal and mold it into the required shape.
EDM machining has its roots in the use of electrical sparks to erode metal, which was first done by scientists in the 19th century. When engineers created high-power devices that could generate enough spark for precise metal cutting in the 20th century, the procedure was further refined. Using traditional machining processes would not be practicable for generating complex forms with the kind of high accuracy cuts that modern CNC EDM machines can do.
Electric Discharge Machining: What Is It?
The machining technique known as “electric discharge machining” (EDM) melts or vaporizes metal using electrical sparks. Electrical discharges between two electrodes that are separated by a dielectric liquid and exposed to different electrical voltages are used to accomplish this cutting procedure. With wire electrical discharge machining, items can be precisely and intricately shaped and contoured in a way that would not be possible with more conventional CNC machining techniques. One benefit is that EDM may be used to mill parts made of materials like heat-treated steels, alloys, and exotic metals, which are typically challenging to produce precisely and with quality control using conventional methods. Complex forms can be produced with extremely tight tolerances using the EDM method. Its ability to precisely carve small holes and narrow slots makes it a priceless tool for manufacturers as well as other engineering applications and sectors.
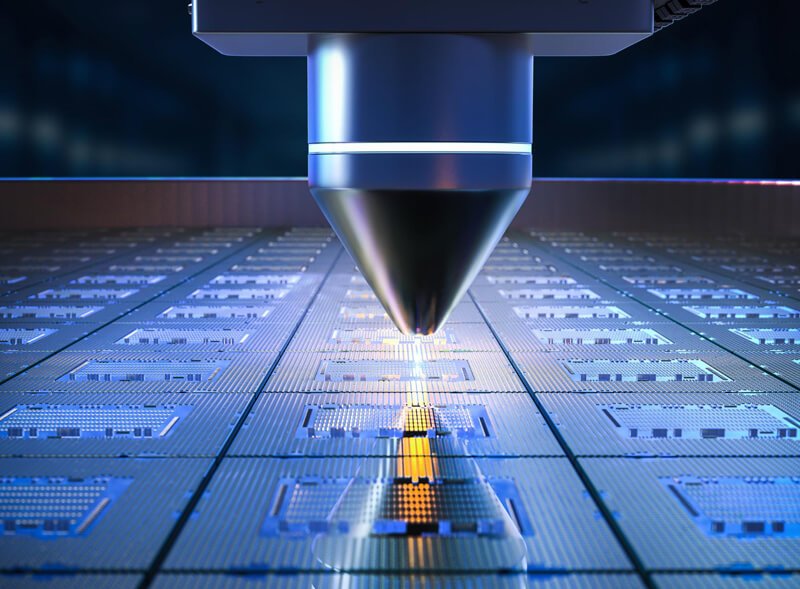
Types of EDM
EDM cutting processes come in three varieties. Among them are:
- Die Sinking EDM –The traditional electric discharge machining method is called die sinking EDM. A die is used in die sinking EDM to produce intricate details. In die sinking EDM, the metal is shaped using a die, which is an electrode composed of copper or graphite. The die is subjected to an electric charge in order to gradually remove the metal. Next, when the extra material is washed away in the dielectric fluid, the die is gradually shifted to achieve the required shape. This technology works especially well for machining intricate shapes that are challenging to produce with other EDM techniques and traditional machining procedures.
- Wire Cut EDM –The wire EDM machining method uses a tiny wire that uses spark erosion to cut through metal, much like a wire cutting through cheese. Sparks are produced between a thin wire and the material to be cut in order for wire EDM to function. The material is eroded by the sparks, producing a clean cut. You may cut complicated patterns and complex forms with this procedure. For some geometries, wire EDM is more economical since it is frequently quicker and more precise than conventional machining techniques. Two-dimensional shapes and pieces with vertical edges are the outcome of involving two axes of motion. EDM wire cutting machines have extremely precise tolerances and can create complicated designs. All conductive metals, including brass, titanium, steel, and aluminum, can be cut with wire EDM.
- Hole Drilling EDM –Electrical discharges are used in the hole drilling EDM method to drill holes in metals. While the procedure is similar to traditional drilling, sparks are produced between the workpiece and electrode utilizing an electrode rather than a drill bit. Tiny portions of the workpiece are melted or evaporated by the spark discharges, allowing it to be further machined to the desired size and shape. EDM hole drilling is a very precise and accurate machining technique that can be used to drill holes in very hard materials. Small, deep cavities can be made in materials via EDM hole drilling.
EDM Machining - Specialty Items
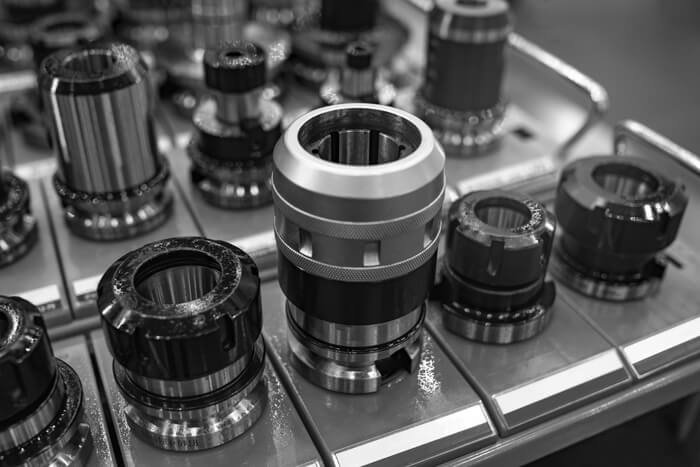
With the highest precision, EDM machining tools and processes can handle large quantities of steel, aluminum, and other metals. EDM machine shops offer wire EDM, hole drilling EDM, and die sinking EDM services.They produce metal components and customized pieces. The process of designing custom parts for EDM calls for accuracy and precision. Engineers can build intricate forms and features with EDM technology that are not achievable with conventional machining techniques. Engineers and manufacturers that want to produce precision parts that satisfy their customers’ demands can find EDM to be a valuable tool since it guarantees a high degree of accuracy and quality while enabling engineers to build parts that precisely match client specifications and requirements.
Applications for EDM Machining
A few industries that use custom EDM parts and Wire EDM machining services include aircraft, aerospace, watercraft, automotive equipment, electronics, medical devices, and circuit boards. For both low and high volume runs, wire EDM services are perfect for unique items that need intricate cuts and shapes or extremely durable material with strict tolerances. Electrical discharge machining produces very thin holes without distortion, making it possible to process delicate areas of custom products.
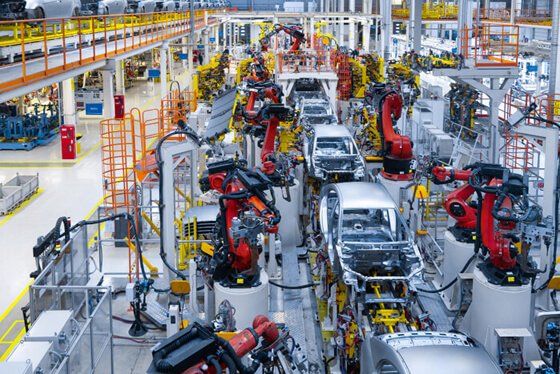
Automotive
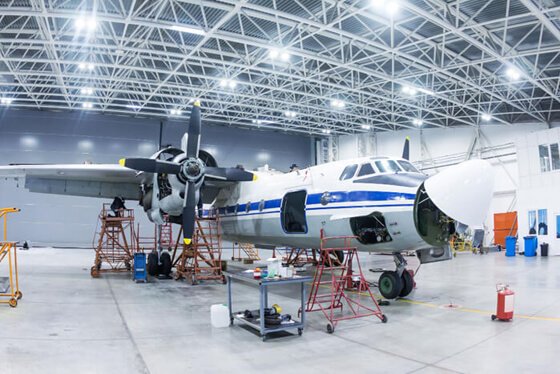
Aerospace
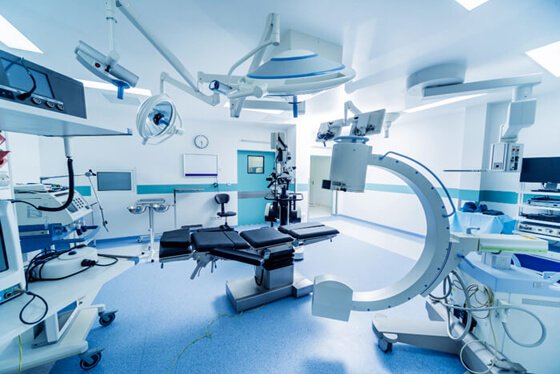
Medical Devices
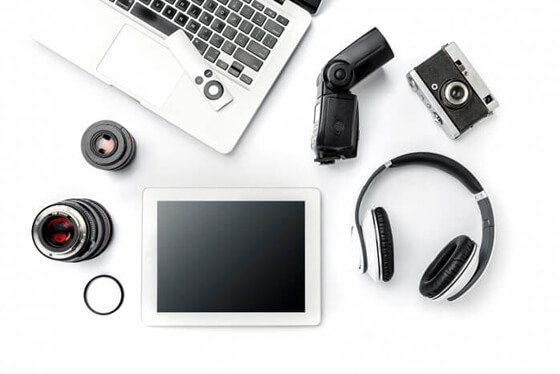
Electronics
EDM Machining Precision Cutting Capabilities Are Used In:
- Tool and Die Making: For creating intricate molds and dies.
- Aerospace: Fabricating complex components with tight tolerances.
- Automotive: Manufacturing detailed parts for engines and assemblies.
- Medical Devices: Producing precise, intricate components for medical equipment.
- Electronics: Crafting small, precise parts for electronic devices.
Advantages of Wire EDM
- Precision Cutting: Ideal for intricate designs and complex patterns with high precision.
- No Tool Wear: The wire doesn’t wear out, ensuring consistent accuracy.
- Fine Surface Finish: Produces a high-quality surface, minimizing additional finishing work.
- Material Versatility: Effective on hard, conductive materials, including exotic metals.
- No Mechanical Stress: The process doesn’t exert force on the workpiece, maintaining its integrity.
- Narrow Kerfs: Allows for very fine cuts, maximizing material usage.
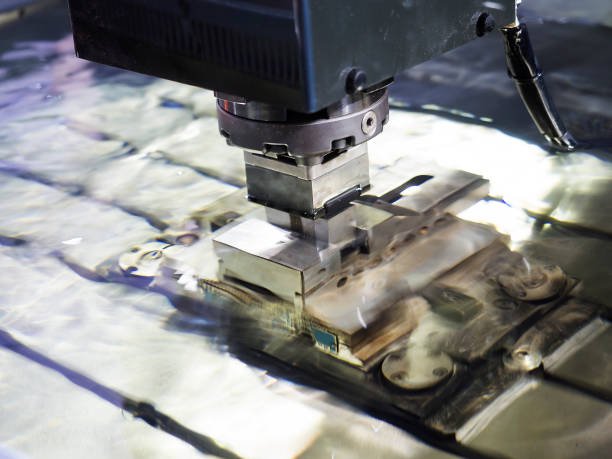
Limitations of Wire EDM
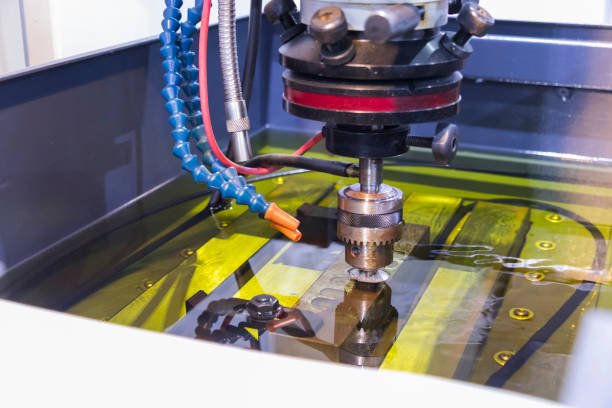
- Material Restriction: Only works on conductive materials.
- Slower Processing Speed: Generally slower than traditional machining methods.
- Higher Operating Costs: Due to specialized equipment and electricity usage.
- Limited Cutting Depth: Not ideal for very thick materials.
- Wire Breakage Risk: Especially with finer wires or intricate designs.
- Post-Process Cleaning: Requires cleaning to remove residues from the dielectric fluid.
EDM Machining Services in Manufacturing
Engineers and manufacturers employ CNC EDM, a powerful tool, to generate precision parts with improved quality, accuracy, and finish. Compared to conventional machining techniques, this procedure allows for more control and accuracy by using electrical sparks to dissolve metal through dielectric fluid. CNC EDM is a fast and effective method of producing intricate forms and features in parts for a wide range of applications. With the variety of power and speed settings that CNC EDM offers, manufacturers may tailor their designs to meet their unique demands. By using this technology as a tool, producers may focus on other aspects of the engineering process by cutting down on the time and effort needed to produce high-quality products.
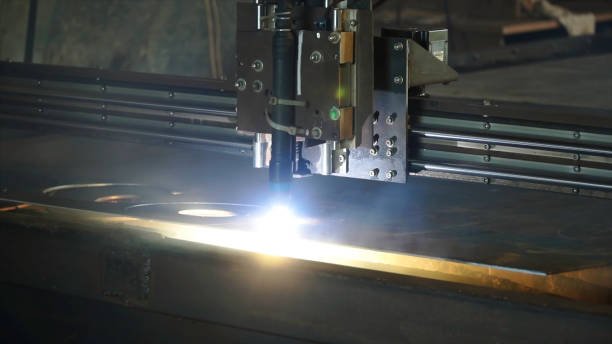
What Our Customers Say
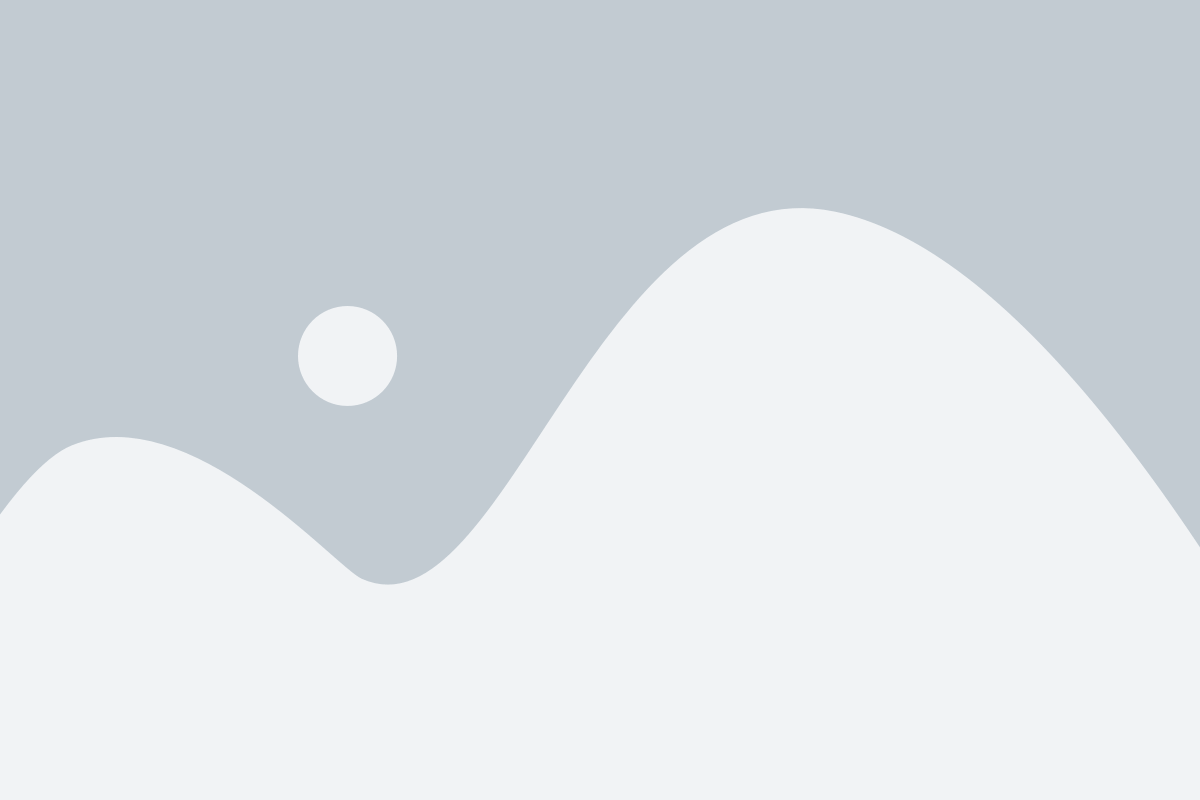
Ready to Elevate Your Project with Precision? Connect with Hacheng Mould Co. Ltd. today for unparalleled mold manufacturing solutions. Don’t wait – your path to flawless precision starts here!